
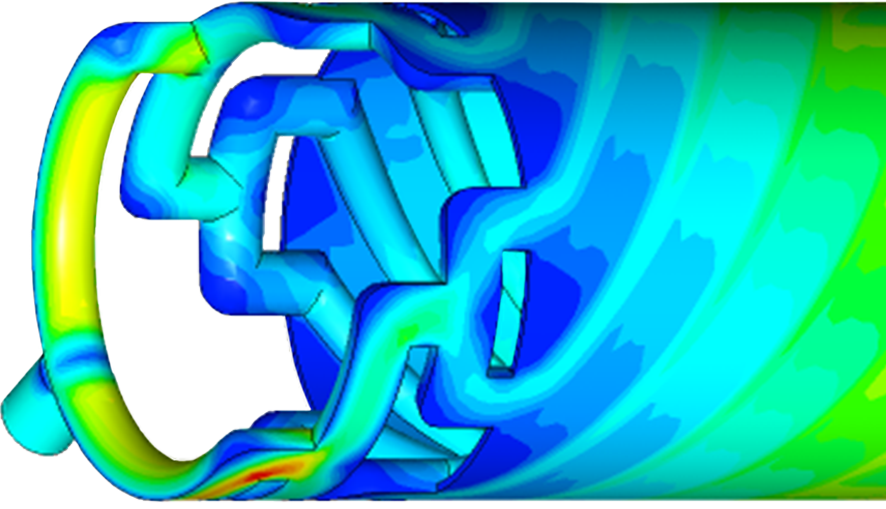
Ansys Polyflow
Ansys Polyflow применяется для моделирования сред со сложной реологией, таких как полимеры, резина, расплавленное стекло, в различных отраслях промышленности.
Ansys Polyflow позволяет анализировать технологические процессы, связанные с обработкой полимеров и производством стекла. Инструмент эффективен для расчета процессов выдувки различной пластиковой тары, термоформововки упаковочных материалов для медицинских и пищевых продуктов, экструзии и соэкструзии при производстве резиновых уплотнений.
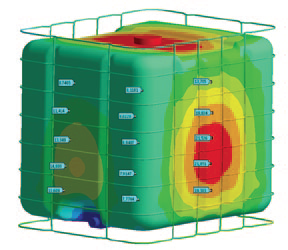
Анализ процессов термоформовки, формования дутьем, штамповки стекла и резины, литья под давлением с учетом вязкокоупругих свойств материала.
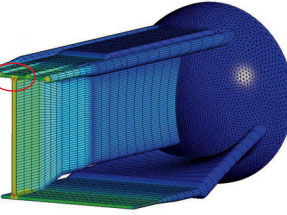
Анализ поведения заготовки, продавливаемой через экструдер поршнем или шнеком, и изменения формы профиля после выхода материала из головки экструдера.
.jpg)
Расчет движения материала при подаче одним, двумя или несколькими шнеками, пропускании через шестеренчатый насос и перемешивании в импеллерных и гравитационных смесителях.

Встроенный алгоритм решения обратных задач для определения формы головки экструдера, требуемой для получения заданного профиля экструдата, вместо традиционного перебора вариантов.
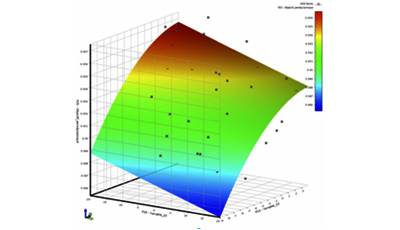
Деформируемые сетки, контроль свободной поверхности, обнаружение контакта, многоблочные сетки, большая библиотека реологических моделей для высокой скорости и точности расчета.
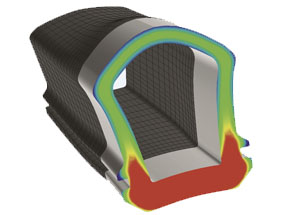
Генерация КЭ-сетки с использованием сеточного генератора Ansys Meshing, анализ результатов с помощью постпроцессора Ansys CFD-Post, параметрические исследования и оптимизация с использованием Ansys DesignXplorer.
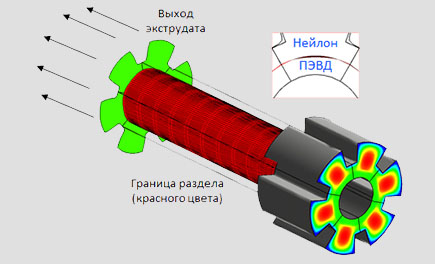
Моделирование соэкструзии – одновременной подачи нескольких жидких полимеров для формирования многослойной структуры – в двумерной и трехмерной постановке.
Решение задачи включает в себя расчет подвижной границы раздела (одной или нескольких) между слоями полимеров с помощью алгоритмов перестроения сетки и декомпозиции расчетной области.
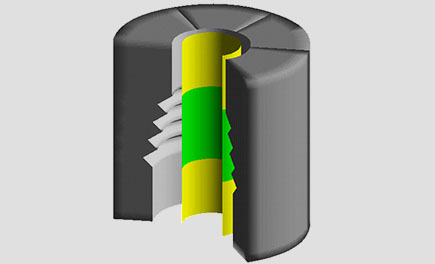
Встроенные средства препроцессинга позволяют воспроизвести весь технологический цикл формования дутьем с заданием начального положения заготовки, смыкания элементов шаблона и раздувания заготовки в шаблоне.
Полученные результаты содержат информацию о распределении толщины в готовом изделии, наличии или отсутствии дефектов, положении и характеристиках технологических швов.
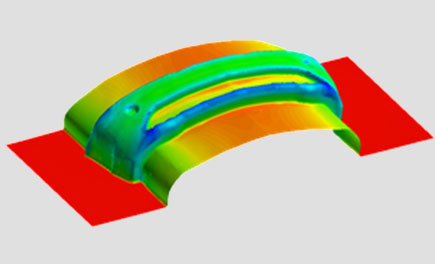
Расчет процесса термоформования включает в себя определение контакта между поверхностью заготовки, формы и штампа, автоматическое переключение граничного условия на сопряжение со стенкой с учетом проскальзывания и теплообмена.
Алгоритм адаптивного сгущения позволяет перестраивать расчетную сетку в момент, предшествующий контактному взаимодействию, а также на последующих этапах решения задачи.
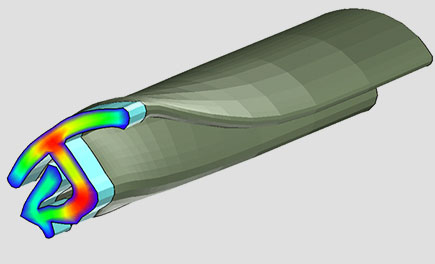
Ansys Polyflow позволяет спрогнозировать масштаб и направленность деформаций экструдата в процессе экструзии и автоматически подобрать необходимый профиль головки.
Корректность решения этой обратной задачи обеспечивается правильным заданием граничных условий на стенках экструдера, а также выбором правильной реологической модели материала.